Open the boot of the car of one of our surveyors and you will find – PPE, measuring equipment and project details for the site being visited. However, in the case of a recent modular build project which was measured and installed ‘off-site’ there were two additions – a map and hiking boots!
New methods of construction are on the rise, one, in particular, is off-site modular build. It affords a speedier way of completing a building – reportedly 30-50% quicker than traditional methods. It causes less disruption as 80% of the build is carried out off-site, with the prepared modules then transported to location, lifted into position ready for final connection. In general, they are more cost effective and have more eco-friendly materials designed-in. The flexibility offered by this method is far greater than most would think and when fully assembled you would never know the building started off life as separate pods in a warehouse resembling a lego set! Money saved on site works can be spent elsewhere, such as highly engineered products, or high spec finishes.
From factory to site – the life of modular build
This project was to be a Hotel situated in an extremely noisy part of London, next to a multi-lane roundabout and main A-road. The well-being, comfort and experience of the guests was of paramount importance, so to ensure a good night sleep, noise was highlighted as a concern by the acousticians.
Despite the specification of high performing new double glazing, internal secondary glazing was also required to provide an additional acoustic barrier to achieve the required level of noise reduction. When it is installed with a cavity of at least 150mm glass to glass, it can reduce noise levels by up to 50dB – the most effective method of acoustic insulation.
Secondary glazing is a retrofit product, generally installed into an existing building which is Listed or in a conservation area. However, it can be of great benefit in new-build projects with high acoustic insulation requirements, to enhance the performance of double glazing to reach the desired levels.
In the case of this method of build there was the opportunity to design in the secondary glazing. This included creating reveals into which the units would be installed. As the secondary glazing would be fitted pre-transportation to site, it was imperative to ensure that when the module was moved, there was no deformation which would undermine the tight fitting of the units and impact on the performance and benefit of the treatment.
The modular pods in the airfield and accompanying map - ready for surveying for the manufacture of the secondary glazing
Arriving at a disused airfield, armed with a map and hiking boots, our surveyor set about making sense of navigating to the relevant pods for measuring. It was a strange experience, walking into what would be hotel rooms with plumbing and wiring in place sitting in the middle of a field. The installation of the secondary glazing will also take place off-site in the factory after decorating is finalised.
When the Hotel is complete and assembled on site, the guests will experience a quiet and relaxing stay with the London hubbub continuing outside; unaware of how the building started out.
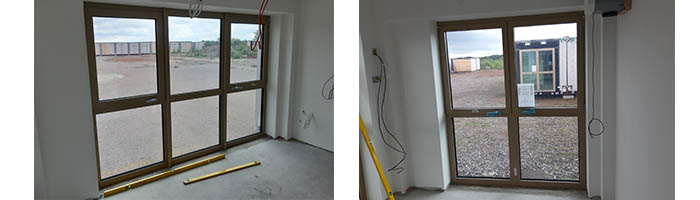
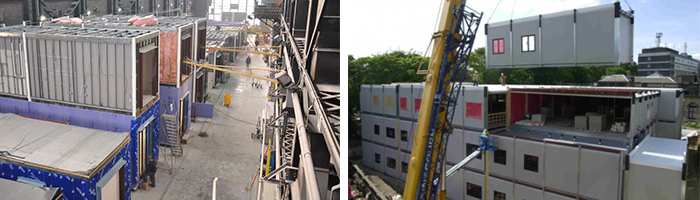
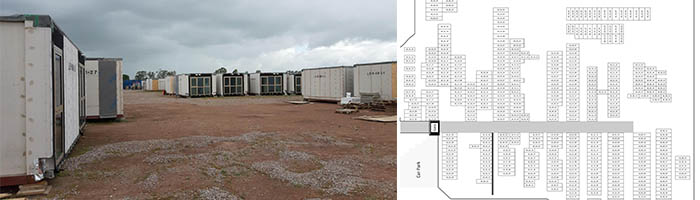
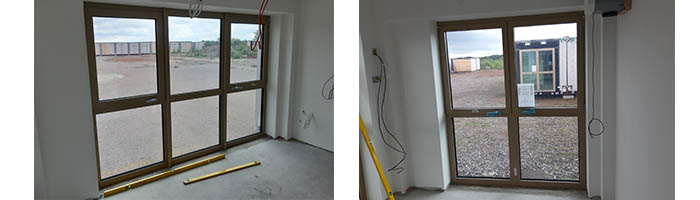
- Date
- Category
- Secondary Glazing in Practice