The two new Kombimatec DGS530 CNC double mitre saws in the Selectaglaze factory have been integrated into the secondary glazing production line with ease, refining the process of cutting aluminium extrusions whilst improving its CNC automation.
The versatile double mitre saw comes complete with 530mm TCT saw blades, a speedier automatic positioning system and motorised heads. The extended cut routine on the saw has ensured that the production team can cope with large aluminium profiles.
The DGS530 comes complete with an overhead colour touch screen, which means that it is away from the working area, making it easier and safer for the operators to load/unload lengths of extrusion. Both machines have been fitted with automatic digital calipers which measure the height of the extrusion and then auto adjust the blade to compensate for the mitre. This has greatly increased efficiencies and reduced processing errors as the operators now do not have to select the correct profile height from a list of over 100 profiles.
DGS30 Overhead colour touch screen operation
More often than not, Selectaglaze curved units are cut at different angles. By simply typing in an angle on the touchscreen, more time consuming manual operations are no longer required.
Furthermore, both machines are also fitted with a cleat cutting facility. Cleat widths can be auto-indexed into the saw. Once the extrusion is loaded to the sawbed, the machine takes over and automatically cuts the whole 6 metre lengths to the pre-set size. Previously it would take over an hour for the operators to manually cut a length. Now, with the DG530’s auto feed trim cutting facility, a width is set on the touchscreen and the machine performs the task in 15 minutes.
DGS30 saw operator
From a sustainability standpoint, Selectaglaze has noticed a significant reduction in profile wastage from the DGS530 because of its improved accuracy and the optimisation of cutting combinations which is an important factor for an in-house fabricator of any size.
The factory has re-tasked one of the old saws into the Timber Shop, so that it can now produce cuts for our timber frames a lot more efficiently.
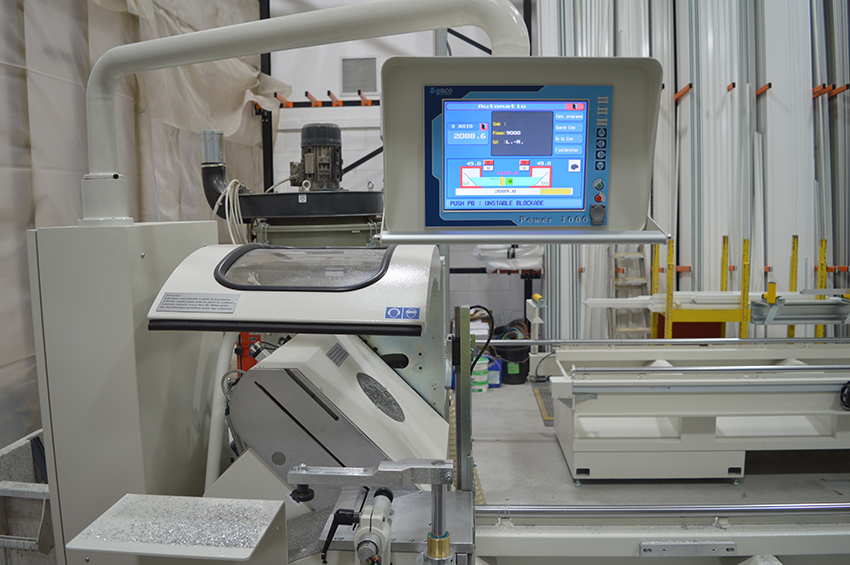
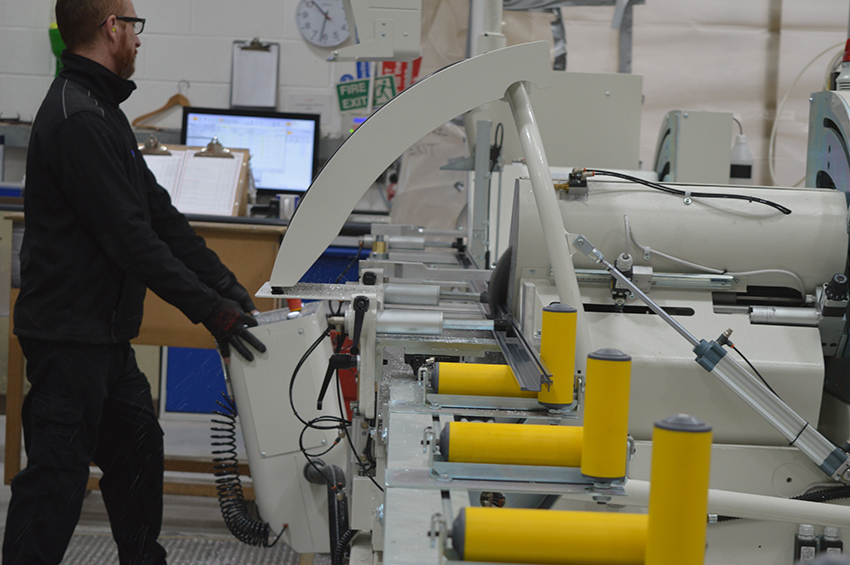
- Date
- Category
- Secondary Glazing in Practice